Un gruppo di studenti dell’università di Roma “La Sapienza” che partecipa al progetto “Motostudent”, ha partecipato ad una competizione universitaria internazionale che vede come evento finale una gara sul circuito “Motorland” di Aragon, in Spagna.
Il loro obiettivo è quello di realizzare un prototipo, in stampa 3D, da corsa di categoria “Premoto3” da far competere contro i team di tutto il mondo.
Per lo scopo, si sono imbattuti nella sfida di dover creare il corpo esterno del motoveicolo, la carena, con il materiale più idoneo per una competizione di questo livello: la fibra di carbonio.
È stato quindi necessario progettare e successivamente eseguire la stampa 3D, master e stampi in PLA.
Master e stampi
Il primo passo che hanno compiuto è stato decidere per quali componenti della carena fare gli stampi e per quali i master. Per quanto riguarda le parti più ingombranti, come fianchi, vasca e cupolino, si sono preferiti i secondi: i master, infatti, ricopiano la forma degli oggetti da stampare, riproducendo con fedeltà le dimensioni, le tolleranze e le caratteristiche superficiali di questi, garantendo una maggiore lavorabilità per il carteggio e, allo stesso tempo, un minore spreco di materiale rispetto a uno stampo tradizionale.
A partire dai master si ricavano successivamente gli stampi veri e propri in fibra di vetro che serviranno per le componenti in carbonio.
Per quanto riguarda le componenti più piccole, è risultato più conveniente progettare e ricavare direttamente gli stampi.
Una volta prese queste decisioni, è stato possibile iniziare il lavoro vero e proprio.
Sviluppo del lavoro per la Stampa 3D
Il lavoro si è articolato in tre fasi:
- Progettazione
- Stampaggio
- Rifinitura
Per sviluppare il prototipo, si sono avvalsi del software di modellazione 3D Inventor, grazie al quale hanno tradotto in formato digitale le idee per i master dei fianchetti.
Ogni dettaglio della fisionomia è stato accuratamente modellato per agevolare le fasi successive. Inoltre, Inventor ha consentito di suddividere i master di grandi dimensioni in parti più piccole, rendendole più adatte alla stampa.
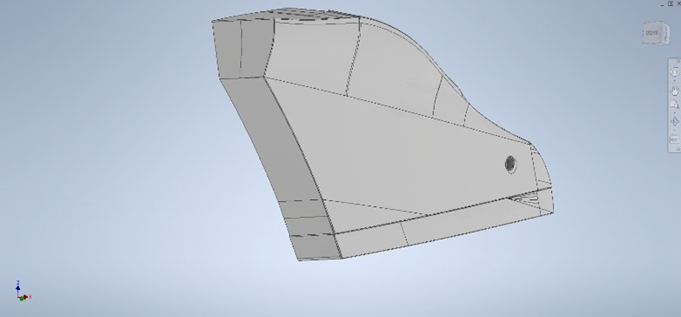
Rappresentazione prospettica del master del fianchetto sinistro della moto su Inventor
Sono così passati alla fase di stampa 3D: grazie alla collaborazione con Make a Shape, che ha fornito i filamenti in PLA necessari per la stampa 3D, hanno stampato (utilizzando i parametri della tabella che segue) e assemblato i master della carena pezzo per pezzo.
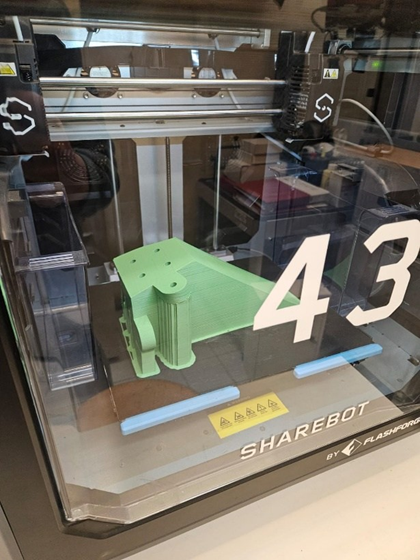
Un componente del master dei fianchetti in PLA appena stampato
Parametri di stampa
Altezza layer | 0.24 |
Numero pareti | 4 |
Numero layer superiori/inferiori | 4 |
Riempimento | 4% |
Tipo di riempimento | Griglia |
Temperatura | 220°C |
Velocità | 200mm/s |
Tipo di supporto | Albero |
Angolo di soglia | 40° |
Riassemblati con meticolosità, i master sono stati poi levigati con l’utilizzo di carte abrasive di grana progressivamente più fine. Le carte sono state leggermente inumidite con l’intento di dissipare il calore generato dall’attrito, il quale avrebbe potuto alterare la qualità del PLA.
Nello specifico, hanno carteggiato seguendo movimenti circolari: questo ha permesso una distribuzione più uniforme della pressione rispetto ai movimenti lineari, andando ad evitare di creare linee o graffi evidenti sulla superficie che sarebbero stati difficili da eliminare e che avrebbero ostacolato la corretta riproduzione dello stampo. Inoltre, i movimenti circolari hanno permesso un maggior controllo e una maggiore precisione su aree curve o complesse.
Una rifinitura perfetta garantisce che i difetti non vengano replicati sugli stampi. I master sono poi passati per le successive lavorazioni.
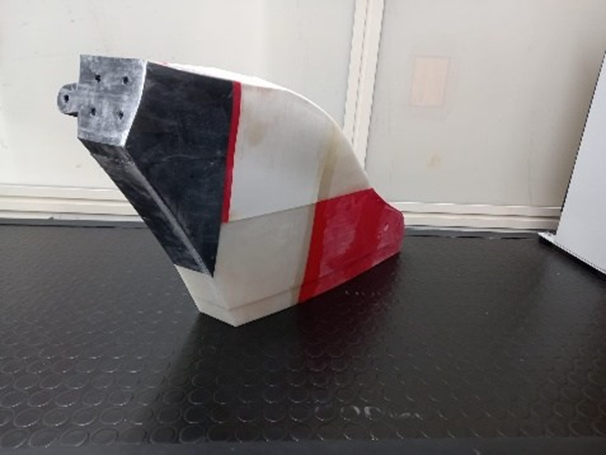
Foto del master del fianchetto sinistro a seguito del carteggio. L’intero fianchetto è stato scomposto in sei parti diverse, successivamente unite. I fori in alto permettono il collegamento con il master del cupolino.
La fase finale ha previsto la realizzazione di stampi in fibra di vetro a partire dai master: si è iniziato applicando il distaccante sulla superficie del master e il gelcoat (questo strato rappresenta la superficie liscia dello stampo ed è essenziale per ottenere una finitura di alta qualità).
Successivamente, la fibra di vetro, altamente resistente, leggera e versatile, è stata tagliata in pezzi adatti alla forma del master, impregnata con resina epossidica e poi posata sul master in più strati, assicurandosi di non generare bolle d’aria.
Infine, si è lasciato indurire lo stampo e, dopo 48 ore, è stato rimosso dal master.
Il componente, svolte delle ultime rifiniture necessarie, è pronto per l’applicazione della fibra di carbonio e la creazione delle nuove carene.
Condividi
info@make-shape.com +39 335 7005054